The benefits of modern LED technology are especially important in those places where luminaires are in continuous operation and where maintenance and repair require a lot of expenditure. Especially for clean rooms, lighting solutions that are highly efficient and that feature a long service life are required. Furthermore, LED luminaires used in these environments must be designed so that they are explosion-protected and comply with strict hygiene regulations.
Sector-specific regulations for clean rooms
In the pharmaceutical industry and the food industry, but also in the semiconductor technology, precision engineering and optics, production processes are carried out under cleanroom conditions, as even the slightest contaminant may render the products useless. Depending on the industry sector and the location, different standards and directives apply that govern the required clean-room technology.
The international standard adopted in Germany as EN ISO 14644-1 is geared to the outdated US standard 209E on the classification of clean rooms and particularly governs the parameters for the semiconductor and aerospace technology. The standard defines the purity levels on the basis of the concentration and the size of the measured particles into nine clean room classes from ISO 1 to ISO 9. In Germany, VDI 2083 applies to the food technology, pharmaceutical, optics and medical industries. The third guiding principle is the guideline on the Good Manufacturing Practice (GMP), which was introduced by US authority FDA in 1962. Different institutions, including the European Commission, adopted these regulations on quality assurance of production processes and production environments.
Increased demands due to explosion protection
A classification pursuant to the clean room classes A to D, defined by GMP, is customary for sterile processes in the pharmaceutical industry. The individual classes define limiting values for the exposure to particle sizes larger than 0.5 and 5 µm, in idle condition and in operating condition. What's more, especially in the pharmaceutical and chemical industry, some of the substances that are processed are combustible liquids or dusts and may form a potentially explosive atmosphere when they react with the atmospheric oxygen.
Although most processes normally take place in closed equipment, the explosion hazard cannot be excluded for certain production steps like filling, or during test runs, maintenance or cleaning. When cleaning agents that contain solvents are used, classification as a hazardous area is required even when no combustible substances are used in the manufacturing process. As a result, explosion-protected luminaires that are suitable for clean rooms are required in this environment as well – luminaires which safely prevent ignition hazards.
Luminaire maintenance in clean rooms is particularly difficult. This means that conversion to LED technology pays off in no time.
The maintenance cost factor
Currently, plant operators mainly use built-in luminaires with fluorescent lamps in explosion-protected clean rooms. With wall or ceiling mounting, deposition of particles on the enclosures of such luminaires and impairment of the air circulation can be prevented. However, this way the expenditure for maintenance and repair is also increased. Further safety features like additional silicone sealing or protective glass may impede access even more. When a luminaire is taken from the ceiling and has to be installed and sealed again after maintenance, this takes a particularly high amount of time and work.
Conventional luminaires with fluorescent lamps have to be maintained every two years. The maintenance interval of so-called long-life luminaires is four to a maximum of five years. Considering the high expenditure and the related downtime, retrofitting of LED luminaires will pay off quickly, when the first maintenance cycle can be dispensed with due to the significantly longer service life of this technology. And often, more than one maintenance can be dispensed with: Modern LED technology has been designed for up to 100,000 operating hours, while conventional lamps achieve only 25,000 up to a maximum of 60,000 hours.
Counting on savings potentials
A calculator can be used to determine the precise savings potential for individual case studies in just a few steps. The calculation includes the costs for investment, operation and maintenance for modern LED luminaires compared to conventional linear luminaires.
Different luminaire types can be selected in a drop down menu and entered in the input mask, with purchase price, quantity, daily operating time and the energy consumption. Then the Return On Investment (ROI) and total Cost of Ownership (TCO) is calculated for the lighting options. The calculator shows the results in the form of a table and in diagrams.
Design feature: Surface roughness
On the basis of its proven product families, R. STAHL develops explosion-protected LED luminaires suitable for clean rooms, which feature the same enclosure dimensions as conventional linear luminaires. These solutions are also ideal for demanding applications that pose specific requirements relating to the luminous efficacy, radiation angle and colour rendering.
The major development effort is focused on fulfilling requirements regarding material selection, surface quality and design guidelines which are defined in the regulations of EU-GMP, ISO and EHEDG. The most important requirement specified in all regulations is the demand for easy and residue-free cleaning of all surfaces in the clean room. In addition, the enclosure design must not feature beads, crevices, indentations and undercuts in which dirt or germs may accumulate. Furthermore, it must be possible to clean surfaces and seals with water jets and they have to be resistant to cleaning agents and solvents.
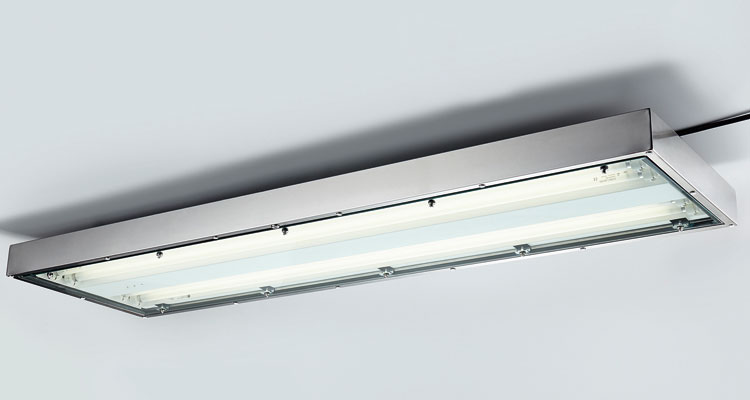
Write new comment